Robot biedt uitkomst voor complexe producten met nauwkeurige afwerking
ZEST heeft dit project uitgevoerd in opdracht van het eveneens in Eindhoven gevestigde Alligator Plastics, producent en ontwikkelaar van kunststof spuitgietproducten.
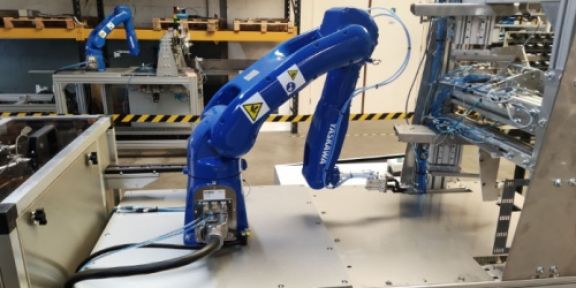
ZEST
ZEST brengt innovatieve systemen en apparaten voor haar klanten op de markt. Door middel van business development, ontwikkeling en financiering kan ZEST ideeën werkelijkheid maken. De ontwikkeling bestaat uit het gebruik van HMI, design en mechatronica, altijd met het oog op het grootst mogelijke succes van het apparaat in de markt. Speciaalmachines worden vooral voor de Nederlandse maakindustrie gebouwd, waarbij ZEST gebruik maakt van jarenlange ervaring om de productie van de klanten beter, efficiënter en dus goedkoper te maken.
Toegankelijk
Voor dit project had ZEST oorspronkelijk gedacht aan de inzet van cobots. Echter, door de gesprekken met Yaskawa kwam ZEST tot de conclusie dat een standaard robot toch beter was voor dit doeleinde in plaats van een van de cobots in het assortiment. De voorkeur ging uit naar een lokale robot producent en een andere klant had ervaring met Yaskawa robots. “Yaskawa bleek erg toegankelijk,” aldus Cyrille Gradus, Commercieel Directeur bij ZEST. “Vandaar dat we gekozen hebben voor Yaskawa.”
Alligator Plastics produceert voor één van haar klanten onder andere spuitgietproducten voor de energievoorziening, specifiek voor groene energie. Bij de ontwikkeling van een nieuwe productrange ontstond de wens om een metalen plaat, voorzien van schroefdraad, in het product te monteren om een voldoende stevige fixatie van het eindproduct te kunnen garanderen. ZEST is voor dit mechanisatietraject benaderd en er werd besloten, vanwege de complexiteit van het product, de gevraagde snelheid van het positioneren en de lastige positie waar het metaal geplaatst moest worden, dat de beste optie was om dit aan de hand van 6-assige robots te doen.
Complex systeem
“Het is een redelijk complex systeem geworden. De afwerk positie van de robot gaat best diep in het product, dus we hebben er een lange gripper op gezet,” vertelt Rens van Hulst, Automation Software Engineer van ZEST. “Met een vision systeem waarmee we in eerste instantie op een lopende band de onderdelen onder de camera door lieten lopen. De robot stond aan het einde van de lopende band om de onderdelen er vanaf te pakken en deze te plaatsen in het product.”
In de praktijk bleek dat producten regelmatig op de lopende band bleven hangen en het kantelen van de producten verliep ook niet altijd vlekkeloos. Uiteindelijk wordt nu gewerkt met een trilvuller, waardoor de producten altijd op dezelfde plek terecht komen. “Op deze manier hoeven we de robot maar één positie in te leren,” gaat van Hulst verder. “De robot krijgt een signaal en dan pakt hij hem op, een veel betere oplossing.”
Trilvuller
Met het oorspronkelijke systeem was er een gebied waarin de robot aan de hand van de camera een pick-positie koos. Deze bewoog mee met de snelheid van de lopende band. “Nu met het uiteindelijke systeem komt het plaatje uit de trilvuller en ons systeem zorgt ervoor dat hij een bepaalde kant op wordt geduwd zodat hij altijd op dezelfde positie blijft liggen. Dan sturen wij een signaal naar de robot en deze pikt het op. Aan de andere kant, waar het product aangeleverd is uit de spuitgietmachine, zal het plaatje dat vanaf de lopende band gehaald is geplaatst worden,” aldus van Hulst. Er zijn twee aflegposities en aan de hand van de aflegpositie die wordt aangevraagd, zal de robot naar links of naar rechts gaan. Bij elke spuitgietronde gebeurt dit vier keer, waarna de vier producten aan de andere kant opgehaald worden door de robot en het proces opnieuw begint.
Lichte producten
Voor dit systeem heeft ZEST gekozen voor de Yaskawa GP7 handling robot, een tamelijk kleine variant omdat er wordt gewerkt met lichte producten van een paar honderd gram. Per machine wordt gebruik gemaakt van één robot maar er zijn drie verschillende machines aan de klant geleverd, dus er wordt in totaal gebruik gemaakt van drie GP7 robots.